Q1. What are the benefits of adopting SUTs?
Single use technologies for biopharmaceuticals are defined as disposable products, which are intended for one-time use, made of various types of gamma-sterilized plastics like polyethylene. They have several advantages over reusable systems because they allow more production flexibility, improve sterility assurance, are more cost-effective, and decrease time-to-market.
- Cost – Reduced manufacturing costs by elimination of cleaning and sterilization steps
- Speed – Time and labor savings during set-up and between operational cycles
- Sterility – Disposable components reduce cross-contamination risks between batches
Adoption and acceptance of SUTs for the development and production of CGTs has also increased for the same reasons—cost, speed and sterility.
Q2. What factors should I focus on when selecting SUTs for CGT manufacturing?
There are many SUTs available for biopharmaceuticals but the majority of SUTs on the market were originally designed for other purposes and have been adapted for CGT processes, thus careful attention and research must be done to qualify their suitability for their intended use prior to selection. Key factors to consider include:
- Sterility – Sterility assurance level (SAL) of 10-6 in order to meet regulatory mandated sterile processing requirements for CGT use
- Low extractable and leachable (E&L) profiles – Cell types used in CGT are highly sensitive to substances that enter the product stream from SUT components; therefore, keeping these levels low can mitigate the impact on product quality and safety
Additionally, the rapidity with which CGTs move through the clinical pipeline means that planning with the end commercialization goals in mind from the beginning can head off any unexpected roadblocks. For example, changes made to a single-use manufacturing component late in clinical evaluation, whether from product discontinuation, lack of scalability, supply chain or validation issues could impose significant delays. Increased costs to substitute and re-validate replacement parts delay timelines and could provide cause for additional regulatory scrutiny of other technologies in the manufacturing process, which all decrease the speed to market. Leveraging the expertise of an established vendor in the space can help mitigate these costly setbacks.
Q3. What are the main types of aseptic fluid connection technologies? What is best for CGT bioprocesses?
Tube welding and aseptic connectors are the two main categories of aseptic fluid connection technologies available. Tube welding is an operation where a tube welder heat-welds tubes that fuse two fluid paths together to create a sterile connection. Conversely, single-use aseptic connectors installed in the fluid pathway achieve this connection through mechanically coupling of two systems. Tube welding has an established history but is a more rigid system best suited for traditional biologics where only a few fluid connections are required and where only one size and type of tubing is used. For some tubing materials, like silicone, which is preferred for CGT manufacturing because of its cost, chemical stability, and low levels of particulates and extractables, tube welding is not feasible for fluid connection since it is only compatible with thermoplastic elastomer (TPE) tubing.
Single-use connection technology offers advantages over tube welding for CGT biomanufacturing in terms of no maintenance required, speed and flexibility of connection. The number of sterile fluid connections required as part of CGT processes can be significantly higher because of the number of unit operations required to produce these complex therapeutics. As well, flexibility in making fluid connections between different tubing sizes and materials is advantageous since many CGT bioprocesses are still evolving and lack standardized technology platforms.
Q4. How do aseptic connectors work?
Aseptic connectors are a significant advancement in the science of connection technology that allows two lines of tubing to be joined, while maintaining a sterile fluid connection in both a sterile and non-sterile environment.
Each connector half is equipped with a protective barrier, usually a sterile membrane, welded across the fluid flow path. When the connector is in place, the protective barrier prevents bacteria and contaminants from entering the fluid pathway while the barrier is in place. The aseptic connectors work by simultaneously removing the sterile membranes from the connector assembly to open the sterile fluid pathway.
They are often supplied as pre-sterilized single-use systems that are ready to use and pre-validated for material biocompatibility, extractables, sterility, and leakage to ensure the connectors do not compromise the product safety and efficacy while being processed.
Q5. What are some key considerations for aseptic connector technology?
Generally, a connector that is robust, simple to use, has few operational steps, and works with a wide range of different tubing types and sizes offers greater operational flexibility to the user.
Aseptic connectors are available in both gendered and genderless versions. Gendered connectors are composed of two different connectors (typically a male and a female component) connected to create the fluid pathway. With genderless connectors, the two connecting parts are identical, so orientation is not an issue. Genderless connectors offer time savings, greater process security, simplified inventory requirements, and increased operational and design flexibility over gendered connections. Genderless aseptic connectors can also form connections between tubing of different sizes across a variety single-use systems, which engenders a more-flexible production platform design. A process that can easily be changed or adapted to a new cell therapy process by simply replacing any of the bag components with either different size bags or a different processing step using the same connection technology can result in a more adaptive process in a field that continues to evolve rapidly.
Q6. How are SUT evolving to meet the unique requirements of autologous CGTs?
Currently, there is a noticeable difference between the scale of traditional bioprocessing and CGT manufacturing. Bioprocessing scales are typically much larger than for autologous CGT products, where smaller batch sizes and volumes are more commonplace. SUT technologies have classically been developed for processing large volume batches of mAbs and other vaccines, but many SUT manufacturers are adapting to the new, small volume requirements for the CGT sector with technologies better suited to smaller production volumes. For example, CPC has developed the MicroCNX® Series Connectors specifically for small-volume CGT and bioprocessing (under 10L). These ultra-compact, aseptic genderless micro-connectors are designed for small volume, closed system processing that eliminate the need for cumbersome multi-step tube welding. Delivering a consistent flow path with every connection using a simple three-step Pinch-Click-Pull connection, MicroCNX connectors are lightweight and help avoid tubing kinks that can affect flow rates. Their size, weight and geometry also fit well with the trend toward compact automated equipment for use in processes like cell expansion.
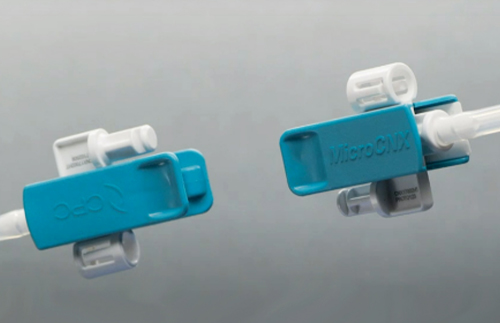
MicroCNX connectors: aseptic micro connectors that provide a simple and efficient solution.